Crane solutions improve efficiency at cement plant
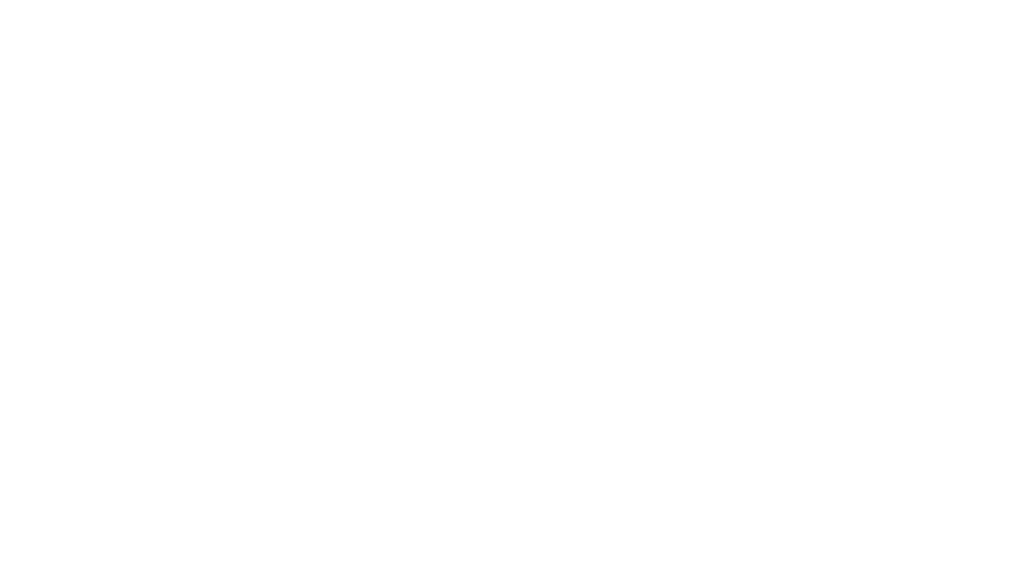
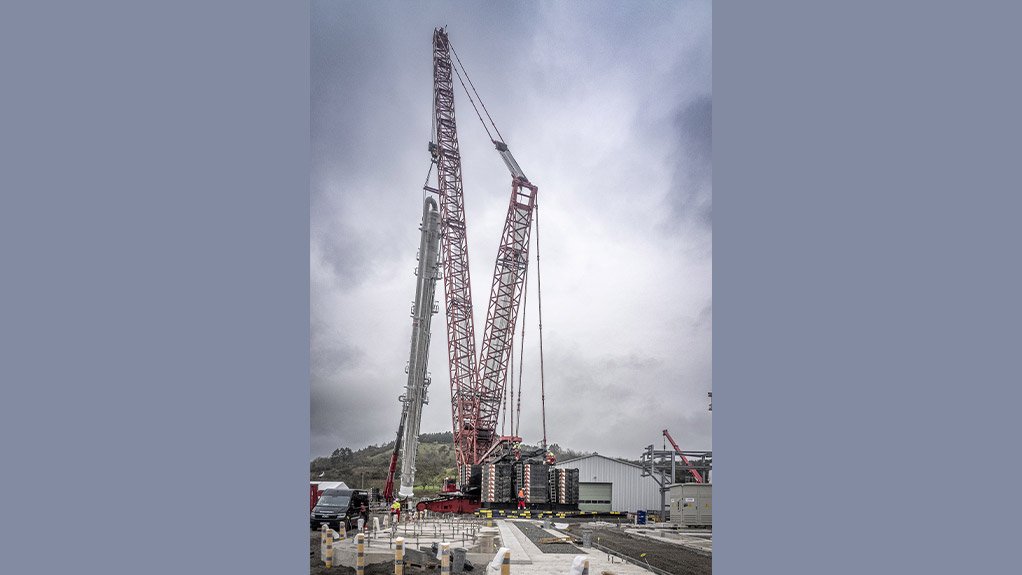
CAP2U PLANT Mammoet has assisted with the efficient and safe lifting and installing of heavy objects for the Cap2U plant at Heidelberg Materials’ Lengfurt cement plant
The efficient and safe installation of heavy objects for a world-first, large-scale carbon capture and utilisation plant for building material manufacturer Heidelberg Materials is under way, with the assistance of heavy lifting and transport solutions company Mammoet.
Under the name ‘Capture-to-Use’ (Cap2U), Heidelberg Materials and engineering company Linde established a joint venture (JV) for the construction and operation of a CO2 capture and liquefaction plant, which is currently being built on the site of the Lengfurt cement plant. The plant is being planned and built by Linde Engineering.
Mammoet was chosen by Linde Engineering to assist in the development of a lifting and installation concept for the various heavy and sizeable components needed for the Cap2U plant.
This concept included the delivery of the large components to the construction site, the planning of areas for pre-dressing within the swing radius of the crawler crane, as well as the crane setup and heavy lifts.
Mammoet analysed and examined various solutions, conducting a feasibility study a year before execution to ensure that workflows, interfaces and construction progress were planned in a precise manner.
In its early involvement, Mammoet’s team was able to provide recommendations for adapting the layout of the Cap2U plant to the requirements of the installation. Additionally, the space requirements were integrated into the overall construction site logistics. This later enabled a safe, efficient and smooth execution, saving the JV time and costs.
Mammoet used a three-dimensional (3D) model of the existing cement plant to leverage its own engineering platform, Move3D, to visualise the complex processes, space requirements and potential interfering edges at the confined construction site. This visualisation provided a better understanding of the planned moves for all affected parties and made coordination easier.
Additionally, the use of a 750-t crawler crane proved to be the most flexible and efficient method of lifting and installing large components safely and on time at the site. Further, with the 3D planning, the parties could ensure that crawler track for the crane would be kept as small as possible, minimising the impact of lifting operations.
Crane Solutions
A 100-t absorber column was erected on the pre-dressing area using a tandem lift. The load was swung almost 180º on the hook of the crawler crane and moved about 20 m to the installation position. There, the column had to be carefully guided behind a building before it could be positioned, aligned and bolted onto the foundation in the steel structure.
Owing to the 55-m length of the absorber column and the high complexity of the lifting process, this was the most challenging heavy lift.
Following this, the 67-t stripper column, four tanks each weighing 72 t, and the 178-t heat exchanger were installed.
Mammoet notes its crawler crane solution offered several crucial advantages. “The crawler crane was flexible enough to safely lift loads of varying sizes and weights over long distances . . . so, intermediate transport on the construction site could be avoided.”
To allow for the pre-installation and parallel construction of the steel structure, the configuration of the crawler crane was changed shortly before the project began. This adjustment saved additional time.
The early involvement of Mammoet, 3D engineering, close supervision of the execution by the on-site planning engineers, as well as the “open, solution-oriented, and trustful collaboration” significantly contributed to a successful project.
Comments
Press Office
Announcements
What's On
Subscribe to improve your user experience...
Option 1 (equivalent of R125 a month):
Receive a weekly copy of Creamer Media's Engineering News & Mining Weekly magazine
(print copy for those in South Africa and e-magazine for those outside of South Africa)
Receive daily email newsletters
Access to full search results
Access archive of magazine back copies
Access to Projects in Progress
Access to ONE Research Report of your choice in PDF format
Option 2 (equivalent of R375 a month):
All benefits from Option 1
PLUS
Access to Creamer Media's Research Channel Africa for ALL Research Reports, in PDF format, on various industrial and mining sectors
including Electricity; Water; Energy Transition; Hydrogen; Roads, Rail and Ports; Coal; Gold; Platinum; Battery Metals; etc.
Already a subscriber?
Forgotten your password?
Receive weekly copy of Creamer Media's Engineering News & Mining Weekly magazine (print copy for those in South Africa and e-magazine for those outside of South Africa)
➕
Recieve daily email newsletters
➕
Access to full search results
➕
Access archive of magazine back copies
➕
Access to Projects in Progress
➕
Access to ONE Research Report of your choice in PDF format
RESEARCH CHANNEL AFRICA
R4500 (equivalent of R375 a month)
SUBSCRIBEAll benefits from Option 1
➕
Access to Creamer Media's Research Channel Africa for ALL Research Reports on various industrial and mining sectors, in PDF format, including on:
Electricity
➕
Water
➕
Energy Transition
➕
Hydrogen
➕
Roads, Rail and Ports
➕
Coal
➕
Gold
➕
Platinum
➕
Battery Metals
➕
etc.
Receive all benefits from Option 1 or Option 2 delivered to numerous people at your company
➕
Multiple User names and Passwords for simultaneous log-ins
➕
Intranet integration access to all in your organisation